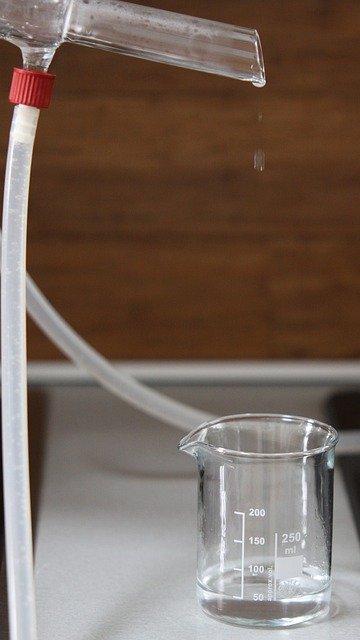
Steam distillation and production of essential oils. Tips, explanations.
The steam distillation is a technique that allows extraction of essential oils and aromatic waters (also called “hydrolates”) from aromatic herbs and from medicinal plants; in other words, with the distillation in a current of steam aromatic waters are obtained from which the essential oil is separated (in most cases by floating on the surface) due to the difference in specific weight and its very low solubility in water.
The steam distillation and then uses the steam as a vehicle to extract as much essential oils that hydrolates from essenziere plants: the final product is a liquid extract obtained by the condensation of steam.
Distillation in a current of steam and essential oils
Steam distillation is only one of the methods to produce aromatic waters, but it is the only one, in addition to the process of squeezing the epicarp of the fruits of the genus Citrus, through which the product known as essential oil is obtained.
In general, we can say that the fundamental structure to carry out the steam distillation is the following:
- A source of heat, such as a wood or gas fire, or in industrial and semi-industrial plants, the electricity needed to heat the plates of a steam generator. In the domestic environment it could be represented by a gas stove or an electric heating plate;
- A boiler, which can be a closed pot containing the water that is transformed into steam (preferably in stainless steel), or a real own steam generator. At home it is possible to adapt a steam cooker;
- A connection pipe, which connects the boiler to the alembic and transporting the steam;
- The alembic, that is the structure that contains the plant material from which to extract the essential oil. The alembic is also called the loading chamber and can have variable volume, depending on the type of system: at home you can have stills with 1-2 L loading, at an artisanal and semi-industrial level from 50 to 1000 L. Also in this case, the best material for the still is stainless steel. The plant material, depending on the type, can be used fresh or even dry, whole (as in the case of shrub plants) or shredded (to favour the release of essential oils: this is the case of oils obtained from wood);
- A condenser, preferably a serpentine, jacketed with cold water (usually mounted at the top of the still), through which the vapour and essential oils pass in the gaseous phase; inside the condenser thus cooled, the water vapour and essential oils return to the liquid phase;
- a decanter, or collection vessel, which can be a Florentine vase or a separating funnel, inside which to collect what comes out of the condenser ( eluate ). The collected eluate will gradually separate into two phases: an aqueous one below (the hydrolat) and a more superficial one (the essential oil).
In the following example, we see how it is possible to produce essential oils at home using a pressure cooker as a boiler : in this case the production of steam takes place inside the pot itself, which contains the water and plant material, separated from a trellis.
This technique, with the boiler not separated from the alembic, is however not recommended: the heat of the fire, used to generate the steam, will in fact also heat the steel walls of the alembic, causing excessive heating of the plant inside, with the risk of obtaining an essential oil with a burnt hint. This risk is not run instead when using extractors in which the boiler is physically separated from the alembic.
Producing essential oils is not at all easy, especially in the home. The yield of essential oils is in fact very low (on average 0.2-0.4%, or 2-4 mL per kg of plant) and it may take several kg of plant (or several extractions) to obtain even just the classic 10 mL of product. In particular, at home it becomes extremely expensive to produce essential oils of lemon balm, helichrysum, yarrow or chamomile, the yield of which is further lowered (0.01-0.03%, or 1-3 mL of essential oil every 10 kg of plant).